Кръстосаните ролкови подhari, като основен компонент, широко използван в механичното оборудване, имат пряко влияние върху производителността и срока на служба на оборудването поради техната стабилност и продължителност. Всъщност, различни проблеми могат да възникнат по време на техната работа, които произтичат от фактори като работна среда, избор на материал и производствени процеси. Тази статия цели да предостави анализ на тези проблеми и съответните решения, за да помогне на читателите да разберат по-добре и да поддържат тази важна механична част.
I. Анализ на проблемите при кръстосаните ролкови подhari
- Недостатъчен капацитет за носене на тегло : Когато се подложат на тегла, превишаващи техния рейтингов капацитет, кръстосаните ролкови подhari могат да пострадаят от деформации, повреди и други проблеми. Този недостатък може да резултира от проектирански дефекти, неправилен избор на материал или операционни изисквания, които превишават възможностите на подhаря.
- Пресилен нагрев : Премногото въртене при липса на достатъчно смазка или чрезмerno внутренno трение можe да доведeт до премерно повишенa температура на подшипниките. Това може да намали техния ресурс и потенциално да причини авария на оборудването.
- Недостатъчен или прекален смазък : Адекватната смазка е от съществено значение за гладкото въртене на подшипниците. Всичко пак, както недостигащата, така и излишната смазка могат да предизвикат проблеми. Недостатъчната смазка може да увеличи триенето и изнасянето, докато прекалената смазка може да води до протичане на мазнина и увеличено триенo съпротивление.
Грешно монтиране : Грешно разполагане или методи на монтиране по време на процеса на инсталиране могат да предизвикат проблеми като несъответствие на подшипниците и вибрации, които влияят върху нормалното функциониране на оборудването.
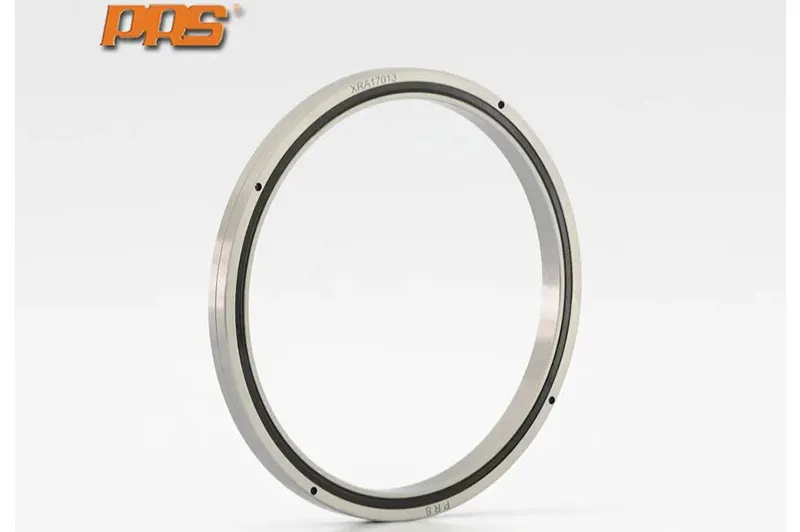
II. Решения за проблеми с кръстосани ролкови подшипници
- Повишаване на капацитета за натоварване : За да се подобри носещата способност на подлагането, е важно да се гарантира нейната носеща способност чрез правилно проектиране и избор на материал. Освен това, разглеждането на усилени конструкции на подлагането може да подобри неговата стабилност при товар.
- Задържане на управлението на смазването : За да се предотвратят повреди на подлаганията поради проблеми със смазването, е критично да се засилят практиките за управление на смазването. Това включва избор на подходящи гуми, осигуряване на своевремено добавяне на смазка и регулярно проверяне на състоянието на системата за смазване, за да се гарантира оптимално смазване на подлаганията.
- Контрол на температурния напредък : Прилагането на по-ефективни конструкции за отнасяне на топлина и избор на подходящи методи и материали за смазване могат да помогнат за контролиране на повишаването на температурата на подлаганията. Това намалява триенето и допринася за по-ниски температури при работа.
- Внимание към процеса на инсталиране : При монтирането на кръстосани ролкови подhari, стриктното следване на инструкцията за монтаж от производителя е необходимо за да се гарантира правилното позициониране, ориентация и други изисквания. Използването на професионални инструменти за монтаж предотвратява въздействие върху подhari-та по време на монтажа, което осигурява точност и надеждност.
- Редовни проверки и поддръжка : За бързо откриване и решаване на потенциални проблеми, регулярните проверки и поддържане на кръстосаните ролкови подhari са необходими. Тези проверки трябва да включват функционирането на подhari-та, ефективността на системата за смазване, повишаване на температурата и други. Своевременните мерки за поддържане осигуряват гладкото функциониране на подhari-та.
Подводейки, тщателното и строго внимание към детайли е необходимо по време на проектирането, избора на материали, монтажа и поддържането на подшипниците, за да се гарантира техната надеждност и продължителност. Чрез непрекъснатите технологични напредъци и подобрения в управлението можем по-добре да гарантираме производителността на подшипниците с кръстосани ролкери и да подобри mej стабилната работа на механичните уреди.